Compressed air and gas monitoring is essential for efficient compressed air and gas systems
- Performance and Reliability
- Energy efficiency and cost savings
- Product quality and safety
- Cleanliness requirements according to ISO 8573
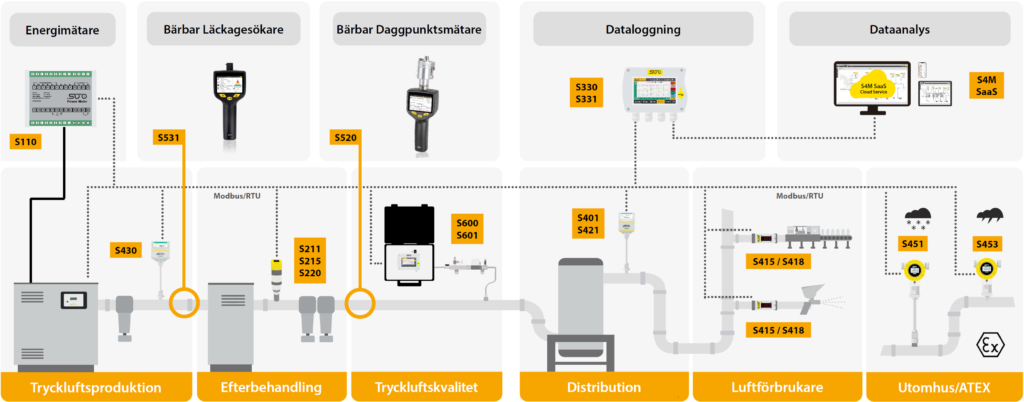
Energy efficient compressed air production
At the production stage, the power consumption of the compressor(s) is measured continuously so that alarms can be triggered if the energy consumption exceeds a certain limit. This is useful information that can be used to see how efficiently compressors are producing compressed air. It compares the ratio of energy consumed to total air flow. The instruments used are Energy meters model S110 which are easily installed without interfering with the compressor. In addition, a pitot tube flow meter model S430 is installed, which is capable of measuring untreated wet compressed air.
In the post-treatment stage, after the compressed air dryer, the dew point of the air is measured to see if the drying process is working. This provides an indication/alarm when the drying equipment is not drying efficiently and needs to be serviced or replaced, before it affects other parts of the compressed air system.
Air quality control according to ISO 8573-1
The dew point transmitters S211/S215/S220 are used for continuous measurement (model depending on dew point level). In addition, the portable dew point meter model S520 is used to temporarily measure the dew point at various points in the compressed air network to ensure that the dew point remains within acceptable levels.
On the outgoing line from the compressed air center, the compressed air quality is measured according to ISO 8573-1, which regulates the various compressed air classes for different types of industries. Where compressed air is used in the production of goods, it is of the utmost importance that the air does not exceed the levels of dew point, oil content and particle content of the various classes. For pharmaceuticals and food/beverage production, it is particularly important that the compressed air is monitored in real time from the compressor center, as well as at regular intervals on the main network in the factory, all to minimize the risk of having your final product spoiled due to poor air quality. Fixed installed air quality measurement equipment is the model S601 and the portable model S600 for occasional measurements and during compressed air quality audits conducted at regular intervals. The S600 generates a report of the measurement that can be stored and sent to the end customer in case a third party performs the measurement.
How much compressed air is used?
In the outgoing air line with dried and filtered air, the air flow is measured with model S401 (plug-in model) or S421 (in-line model). This is to get control of the total air produced. Flow meters are installed at each consumption point to provide information on what each machine/other consumes. The total sum of each consumption point must be compared with the sum from the meter that measures the air in the outgoing air pipe (from the air center. If the difference is too large, an alarm should be triggered that there is a leak in the truck air network and it is time to look for leaks with the S531 or S530 leak detector. If you have a large compressed air network, divide the network into compressed air zones by installing more flow meters of the S401/S421 model. Then you know in which zone the leak has occurred, which saves time and money to quickly find and fix the leak.
Call us for a consultation, or fill in the form below and we will contact you.
Sweden: +46 10 130 10 00
Norway: +47 55 55 86 99