ISO8573-1 is an international standard for the quality of compressed air. It defines the maximum permissible levels of contaminants, such as oil, water and particles, that may be present in compressed air. This standard is used to ensure that compressed air used in industrial processes is clean and free of impurities that could damage equipment or affect the quality of the finished product.
The standard is divided into several classes, each class defining different maximum permissible levels for different pollutants. For example, Class 1 defines the highest level of air cleanliness, with very low levels of pollutants allowed. Class 2 is slightly less clean and so on. See table for definition of the different classes;
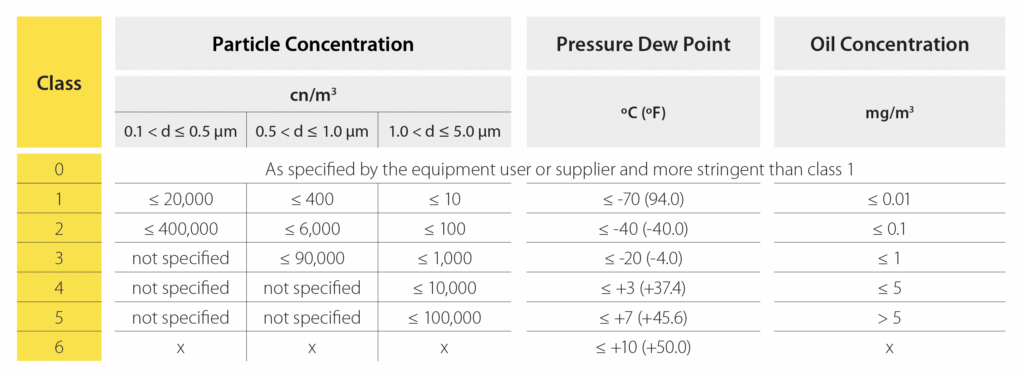
One of the key benefits of ISO8573-1 is that it helps ensure that compressed air used in industrial processes is clean and free of contaminants that could damage equipment or affect the quality of the finished product. This can help reduce downtime and maintenance costs, as well as help improve the overall efficiency of the process.
In addition to the standard, it is also important to regularly test and monitor compressed air to ensure that it meets the requirements of ISO8573-1. This can be done using specialized test equipment, such as particle counters, oil mist detectors and humidity analyzers (dew point sensors).
In conclusion, ISO8573-1 is an important standard for the quality of compressed air that helps ensure that industrial processes are safe and efficient. By regularly testing and monitoring compressed air to ensure it meets the requirements of the standard, companies can help reduce downtime, maintenance costs and improve the overall efficiency of their processes.
How do you measure impurities in compressed air and which measuring instruments are needed?
Portable instruments and permanently installed instruments are both commonly used to validate compressed air quality, but each has its own unique characteristics.
Portable instruments, which include particle counters, oil and dew point sensors, are designed for use in a variety of environments such as point-of-use testing or temporary measurements on the compressed air discharge line from a compressor station. These instruments are typically smaller, lightweight and easy to transport for use in a variety of locations. Portable measuring instruments is often an integral part of service companies that perform annual or monthly checks of compressed air systems at their customers. A portable measurement device should also generate an automatic pdf report that makes it easy to deliver a traceable report to the customer after the analysis is completed.
Permanently installed instruments for particle counting, oil and dew point measurement are typically used for continuous monitoring of compressed air quality. They are installed directly in the compressed air system, preferably at the outlet of the compressor center where the air is dried and filtered, and are connected to a control system that allows real-time monitoring and data analysis. These instruments provide a permanent and reliable solution for compressed air quality validation. Recommended for applications where compressed air quality is critical and continuous monitoring is required to ensure that contaminated compressed air is never used in production. In a pharmaceutical manufacturing facility where compressed air is used in the filling process of injectable drugs, permanently installed instruments are recommended. This is because the quality of the compressed air is critical and must be continuously monitored to ensure patient safety and product quality.
Even in manufacturing facilities where compressed air is used to power pneumatic tools, a portable instrument can be used to test the quality of the compressed air at regular time intervals at various points in the plant, such as in the compressor room, at consumer points and at the end of the distribution lines. This allows the facility to identify and address any compressed air quality issues with high levels of particulates, oil mist or moisture that could cause equipment failure or affect the product quality of a manufactured end product.
In summary, both portable and fixed-installed instruments have their own advantages and disadvantages, and the choice of instrument will depend on the specific application and user needs. Portable instruments are suitable for on-site testing and troubleshooting, while permanently installed instruments are recommended for continuous monitoring and long-term monitoring.
Kompauto Nordic supplies two types of complete measuring equipment in accordance with ISO8573-1. SUTO iTEC S600 is a portable device that is used for temporary audits, either by the end customer himself or by a service company. SUTO iTEC S601 is the permanently installed model for continuous measurement of compressed air used in critical product production.
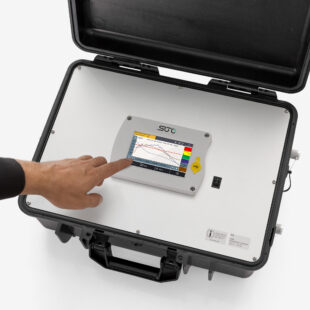
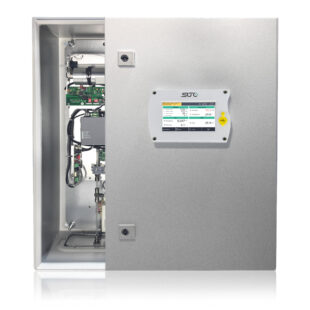